Target in movimento
PolyWorks® aiuta a mantenere la produttività del gruppo di potenza GE
Extreme Fab Inc. opera nel settore della produzione di metalli strutturali. L'azienda dispone degli strumenti e della competenza necessari per costruire gli enormi macchinari destinati all'industria petrolchimica, al settore delle energie e degli autotrasporti. Uno dei suoi principali clienti è GE Aero Energy; questa azienda offre alle imprese e alle comunità di tutto il mondo la possibilità di generare energia in modo affidabile ed efficiente, in prossimità o direttamente nel punto di utilizzo e in qualsiasi momento, in rete o extra rete.
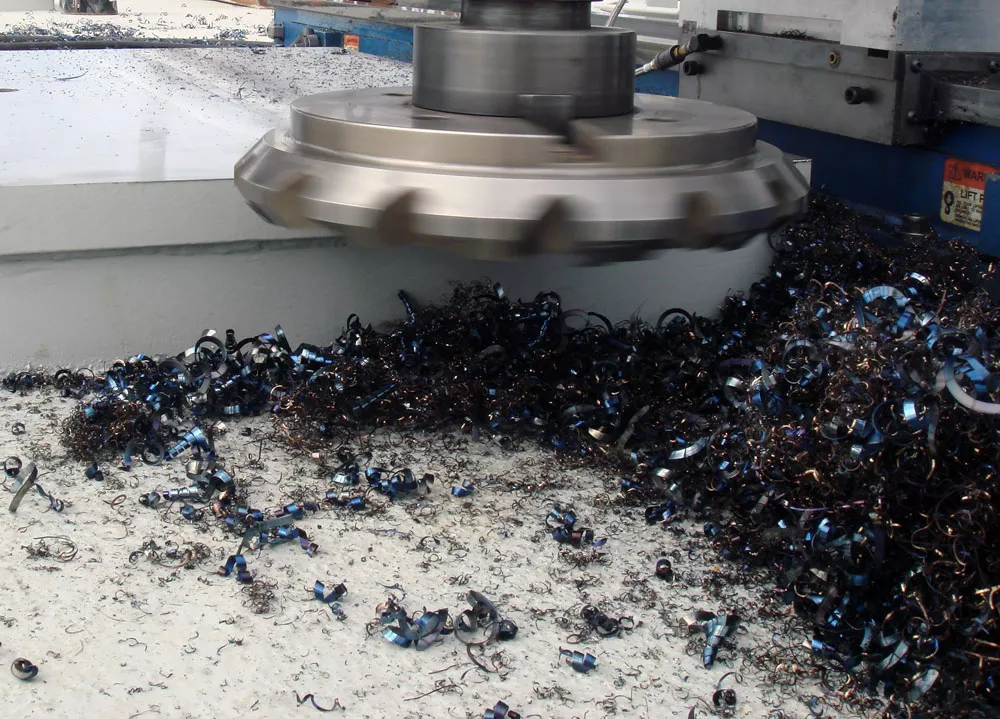
Servendosi di un'ampia gamma di carburanti, la turbina a gas aeroderivata FlexAero LMS100 di GE Aero Energy genera fino a 100 megawatt di elettricità con un'efficienza di conversione pari al 44%. Nata per essere installata e pronta a produrre rapidamente in località isolate, come ad esempio villaggi remoti, siti di perforazione o luoghi di disastri, questa eccezionale turbina è una centrale elettrica racchiusa in una scatola. Il pacchetto LMS100 comprende turbocompressore, turbina a gas e compressore; il tutto montato e preassemblato. Per far funzionare questa complessa opera di ingegneria, viene utilizzato una grande slitta ad alta precisione.
Per la lavorazione delle slitte di GE Aero Energy, Extreme Fab collabora con Dimensional Engineering, che fornisce acquisizioni di dati digitali 3D, servizi di ingegneria e analisi per affrontare le difficoltà tecniche relative alla progettazione e alla produzione in un'ampia gamma di settori e applicazioni.
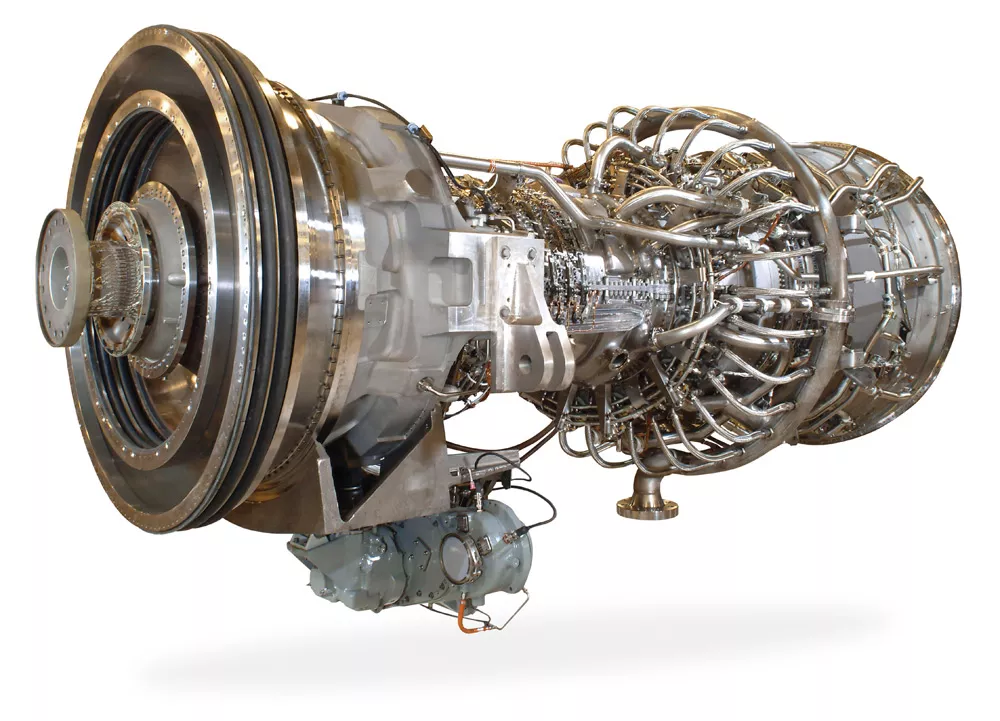
La turbina a gas aeroderivata LMS100 fornisce fino a 100 megawatt di energia elettrica.
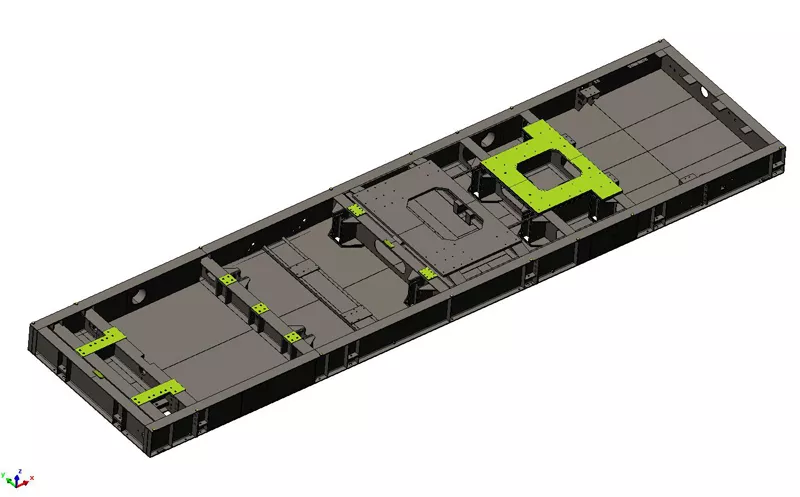
Grafica renderizzata del pattino da 60 x 25 piedi lavorato con macchine di precisione. Le superfici portanti (verdi) vengono lavorate con una tolleranza in planarità pari a +/- 0,002”.
«Ci vogliono migliaia di dollari solo per spedire il pattino; questo significa che se deve essere restituito a Extreme Fab per essere rilavorato, potrebbe essere necessario sostenere decine di migliaia di dollari di costi aggiuntivi solo per le spese di trasporto»
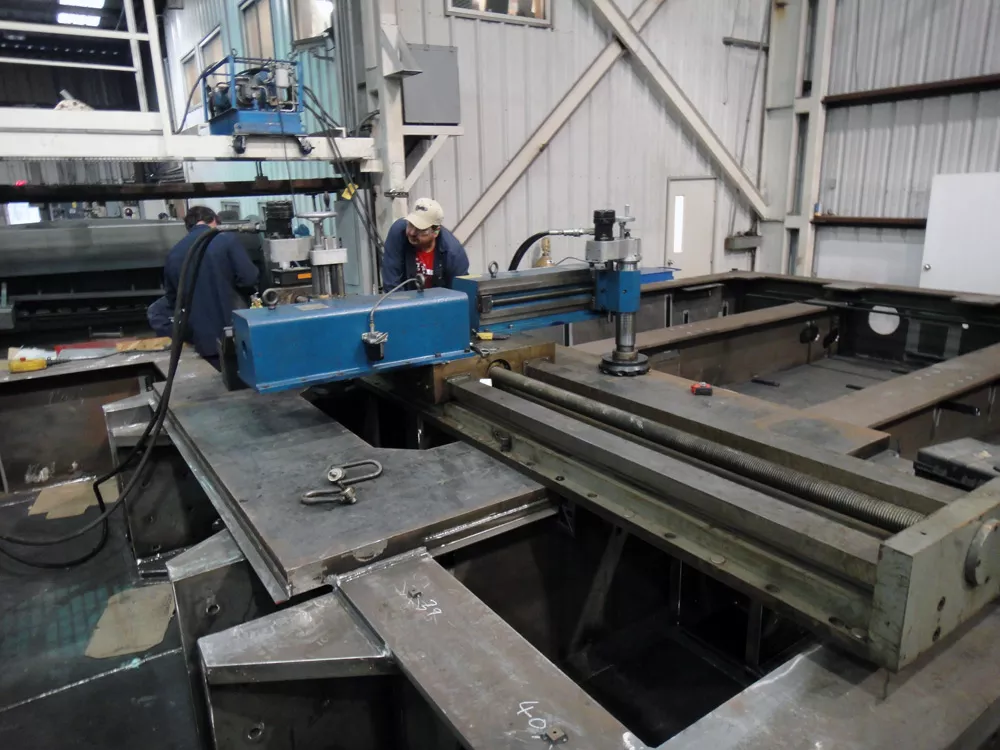
Gli addetti alla macchina effettuano regolazioni al sistema di lavorazione da una tonnellata.
La sfida
Con dimensioni pari a 60 x 25 piedi (18x7.5 metri), la slitta dell’LMS100 presenta superfici di appoggio e fori di montaggio accuratamente lavorati. Anche la più piccola imprecisione nella lavorazione può provocare una diminuzione del rendimento del gruppo di potenza, della produzione di energia e della vita del gruppo. William Bonner, Managing Director presso Dimensional Engineering spiega: «Le piastre di montaggio richiedono tolleranze di planarità di +/- 0,05 mm e tolleranze in altezza di +/- 0,10 mm in tutti i punti presenti nei 18,3 metri di lunghezza del pattino».
La lavorazione di un oggetto così grande e con tolleranze ridotte non è un compito facile, ma la slitta presenta anche ulteriori difficoltà: «Questa cosa si muove; non è mai statica», spiega Bonner. Una macchinario da una tonnellata si appoggia sulla slitta mentre vengono realizzate le lavorazioni di precisione. «Ogni volta che si piazza la fresa sul pattino, si verifica una flessione dovuta al peso che non è distribuito uniformemente».
Nel corso di un lavoro di 12 ore al giorno per 10 giorni, gli addetti alle macchine spostano le apparecchiature provocando sollevamenti, flessioni e torsioni delle piastre di montaggio.
Per complicare ulteriormente le cose, c'è anche la dilatazione termica. Esposto a variazioni di temperatura considerevoli fino a 50°F (10°C) in 24 ore, il pattino si espande e si contrae durante tutta la giornata. «Il compito di Dimensional Engineering è controllare la configurazione e definire le profondità e gli angoli di taglio, per consentire a Extreme Fab di rispondere ai requisiti di precisione di GE», spiega Bonner.
Se il pattino arriva agli stabilimenti di GE e non è conforme alle specifiche richieste, le conseguenze sono gravi: «Ci vogliono migliaia di dollari solo per spedire il pattino sola andata; questo significa che se deve essere restituito a Extreme Fab per essere rilavorato, potrebbe essere necessario sostenere decine di migliaia di dollari di costi aggiuntivi solo per le spese di trasporto», spiega Bonner. Se la rilavorazione ha effetto sulla pianificazione della produzione, le non conformità possono comportare importanti penali economiche.
La soluzione
A ogni spostamento della macchina, prima di ciascun taglio e dopo ciascuna operazione, Dimensional Engineering fornisce a Extreme Fab misurazioni precise per il piazzamento della fresa, dell’utensile di taglio e del pezzo in lavorazione rispetto alla condizione non deformata e non sollecitata del pattino. Senza questo controllo delle misurazioni, sarebbe difficile, se non addirittura impossibile, rispettare le specifiche di GE.
Gli strumenti scelti da Bonner sono i laser tracker FARO, abbinato al software PolyWorks|Inspector™ di InnovMetric. «Usiamo i laser tracker per acquisire misurazioni precise e PolyWorks per studiare e gestire i dati raccolti, per controllare il progetto che è soggetto a continue variazioni», spiega Bonner.
Il team di Bonner, composto da due persone, inizia effettuando un allineamento preliminare del pattino non deformato. Servendosi di 50 target di riferimento saldati al pezzo in lavorazione, il laser tracker misura le entità di riferimento (datum) del pattino, dopodiché viene usato PolyWorks® per creare un sistema di coordinate globali. PolyWorks viene quindi impiegato per definire più sistemi di coordinate locali, che consentono al team di isolare il movimento su una singola piastra di montaggio mantenendo, contemporaneamente, le posizioni relative rispetto all'intero pattino.
«Se non fossimo in grado di controllare le misurazioni tenendo in considerazione il riposizionamento del tracker, andremmo incontro a seri problemi».
Dopo aver posizionato e livellato la fresa, il team di Bonner misura il pattino e il piazzamento dell’utensile di taglio, per fornire i punti esatti, che gli addetti alla macchina useranno per programmare l'angolo e la profondità di taglio. Una volta completata l'operazione, vengono acquisite nuovamente le misurazioni per verificare il taglio prima di un nuovo passaggio.
Dal momento che il pattino varia con la temperatura, il team di Dimensional Engineering elabora tutti i dati di misurazione utilizzando le funzionalità di compensazione dinamica della temperatura offerte da PolyWorks. Questa regolazione abbinata al punto esatto dell'entità lavorata consente agli addetti alla macchina di programmare i percorsi di taglio rispetto al pattino in condizioni di temperatura stabili, anziché nella posizione effettiva che varia in modo dinamico.
Date le dimensioni del pattino e le considerazioni sulla velocità radiale, i laser tracker FARO vengono posizionati decine di volte nel corso del progetto di 10 giorni. Questo aggiunge un'altra variabile alla lavorazione di precisione. Per assicurarsi che tutte le misurazioni siano precise rispetto a tutte le posizioni del tracker, il team di Bonner usa la funzione “sposta dispositivo” di PolyWorks e il bundling in tempo reale. Come dice Bonner: «Se non fossimo in grado di controllare le misurazioni tenendo in considerazione il riposizionamento del tracker, andremmo incontro a seri problemi».
Per finalizzare il progetto, viene condotta un'ultima ispezione per confermare che il pattino risponda effettivamente alle specifiche di GE. «Valutiamo e certifichiamo tutte le misurazioni, sia nel corso del progetto sia prima della spedizione», conclude Bonner.
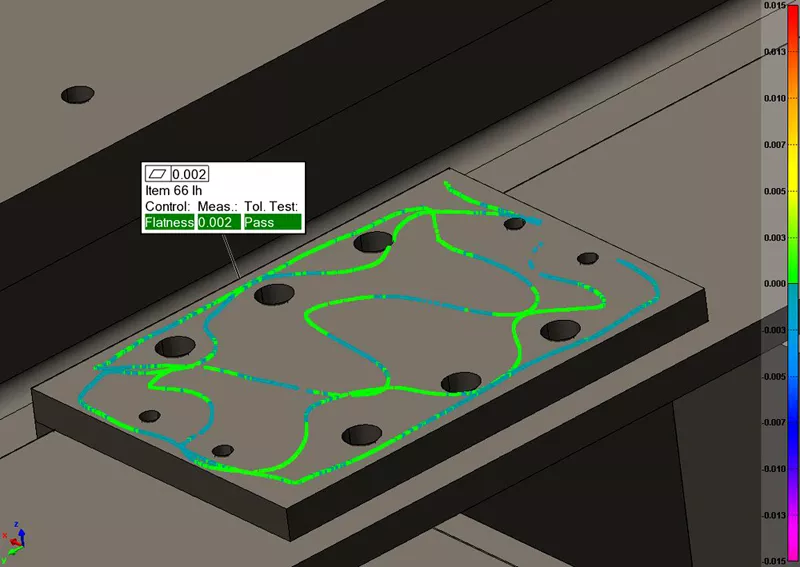
I risultati dell'ispezione finale confermano la planarità di una superficie di montaggio.
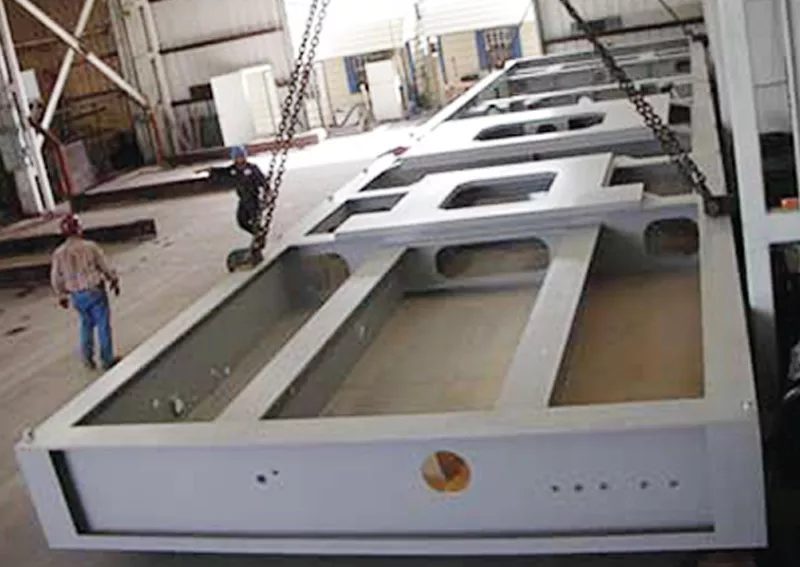
La slitta finita, in fase di preparazione per il trasporto verso gli stabilimenti di GE.
Vantaggi
«Senza l'uso della soluzione laser tracker e PolyWorks|Inspector, non avremmo modo di raggiungere questo livello di accuratezza e precisione, o almeno non in modo quantificabile», spiega Bonner; «Portiamo avanti questo lavoro da sei anni, e abbiamo lavorato su più di 50 slitte. Non è stato necessario rispedirne nessuno per sottoporlo a modifiche». Nel corso di questi sei anni, Dimensional Engineering ha ricevuto solo due rapporti di non conformità: uno era relativo ad un solo foro fuori specifica, l'altro era dovuto a specifiche contrastanti nei disegni del pattino.
Dimensional Engineering applica lo stesso processo e gli stessi strumenti ad altri progetti su vasta scala, tra cui i componenti ausiliari del pacchetto LMS100, tra cui l’intercooler. «Le tecniche che implicano l'uso del pattino servono a posizionare due guide di montaggio del radiatore da più di 15 metri mentre vengono saldate, 120 fori sulla flangia di montaggio del radiatore, il parallelismo dell’ingresso e le flange all’uscita», spiega Bonner. «Senza le misurazioni di precisione che acquisiamo con il laser tracker e PolyWorks, il radiatore non entrerebbe nell’intercooler, e l’intercooler non sarebbe correttamente in sede rispetto alla turbina LMS100».
Con PolyWorks, Dimensional Engineering rende gestibili i target in movimento e consente di prevedere le lavorazioni su larga scala.