Ruchome cele
PolyWorks® pomaga zachować wydajność elektrowni GE
Extreme Fab, Inc. zajmuje się strukturalną produkcją metalową, posiada narzędzia i umiejętności do budowy masywnych maszyn, których potrzebuje przemysł naftowy i gazowy, energetyczny i ciężarowy. Jednym z jej kluczowych klientów jest GE Aero Energy. GE Aero Energy zapewnia firmom i społecznościom na całym świecie możliwość wytwarzania niezawodnej i wydajnej energii w miejscu lub w pobliżu miejsca użytkowania, w dowolnym czasie, w sieci lub poza nią.
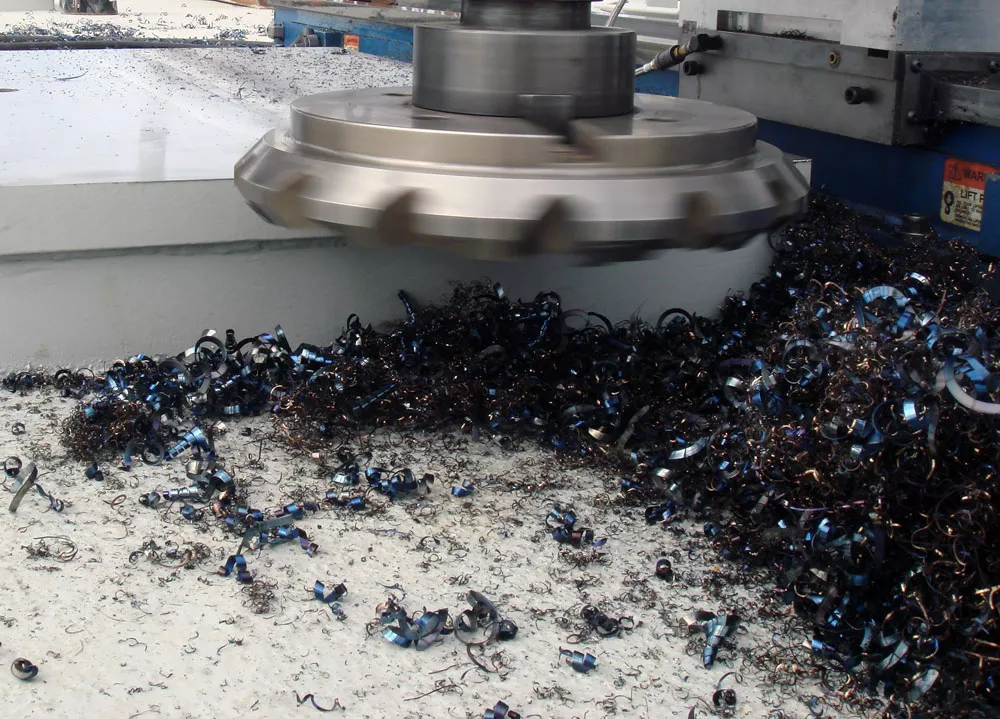
Wykorzystująca szeroką gamę paliw turbina gazowa FlexAero LMS100 firmy GE Aero Energy wytwarza do 100 megawatów energii elektrycznej przy sprawności konwersji wynoszącej 44%. Ta wyjątkowa turbina przeznaczona do szybkiego zamontowania i instalacji w odizolowanych miejscach, takich jak odległe wioski, miejsca odwiertów lub obszary katastrof, to elektrownia w pudełku. Pakiet LMS100 zawiera turbo, turbinę gazową i sprężarkę, zamontowane i wstępnie złożone. Aby ten wyrafinowany system działał, wykorzystuje duży, precyzyjny skid.
W zakresie obróbki skidów dla GE Aero Energy, Extreme Fab współpracuje z firmą Dimensional Engineering, która świadczy usługi w zakresie cyfrowego pozyskiwania danych 3D, inżynierii i analizy, aby sprostać wyzwaniom związanym z projektowaniem i inżynierią produkcji w przeróżnych branżach i zastosowaniach.
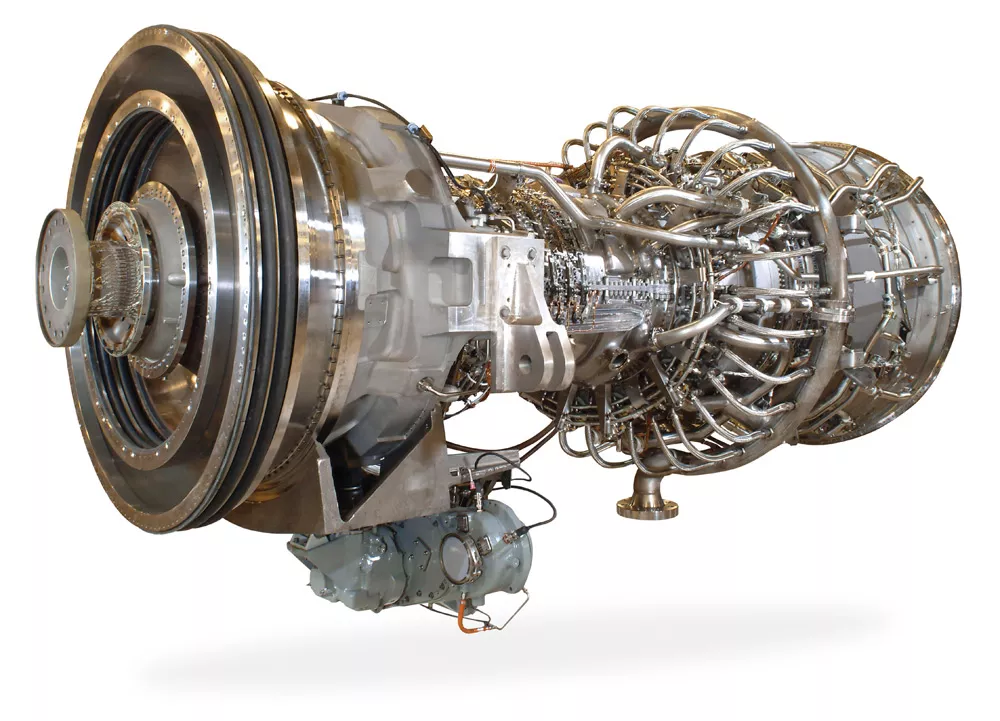
Aerodynamiczna turbina gazowa LMS100 wytwarza do 100 megawatów energii elektrycznej.
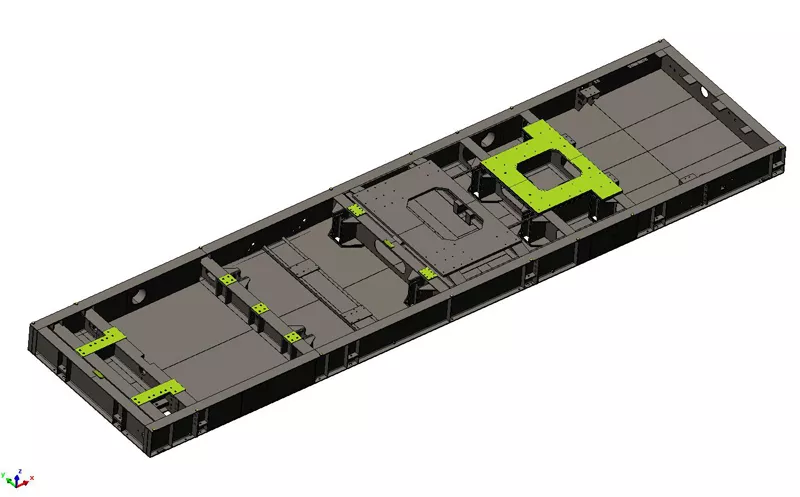
Rendering precyzyjnie wykonanego skida o wymiarach 60 x 25 stóp. Powierzchnie łożysk (zielone) są obrabiane do płaskości +/- 0,002".
„Samo wysłanie skida w jedną stronę kosztuje tysiące dolarów, więc jeśli musi on wrócić do Extreme Fab w celu wprowadzenia poprawek, to same dodatkowe koszty transportu mogą wynieść dziesiątki tysięcy dolarów”.
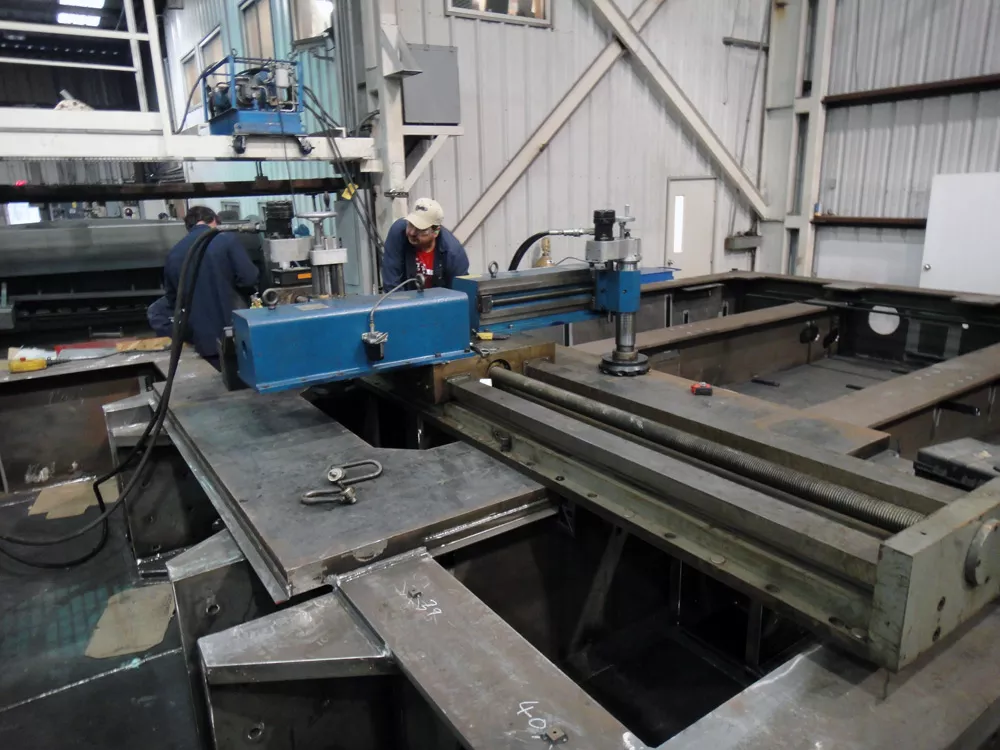
Operatorzy dokonują regulacji jednotonowego systemu obróbki w terenie.
Wyzwanie
Mierzący 60 na 25 stóp skid LMS100 ma precyzyjnie obrobione powierzchnie łożysk i otwory montażowe. Najmniejsze odchylenia w obróbce mogą obniżyć sprawność operacyjną elektrowni, jej wydajność energetyczną i żywotność. Według Williama Bonnera, dyrektora zarządzającego ds. inżynierii wymiarowej, „podkładki montażowe wymagają płaskości +/- 0,002" i wysokości do +/- 0,005", w odniesieniu do wszystkich punktów na całej 60-stopowej długości skida”.
Obróbka dużego obiektu z taką precyzją to niełatwy wyczyn, ale skid stanowi jeszcze większe wyzwanie. „Skid stale się porusza; nigdy nie stoi w miejscu” — mówi Bonner. Jednotonowe systemy do obróbki w terenie umieszcza się na skidzie podczas wykonywania precyzyjnych cięć. „Za każdym razem, gdy umieszczamy frezarkę na skidzie, ugina się on, ponieważ ciężar frezarki nie jest równo rozłożony”.
Przez 10 dni, 12 godzin dziennie operatorzy przemieszczają sprzęt, powodując, że podkładki montażowe podnoszą się, opadają, skręcają i obracają.
Czynnikiem, który dodatkowo komplikuje zadanie, jest również rozszerzalność cieplna. Przy znacznych wahaniach temperatury, sięgających 10°C (50°F) w ciągu doby, skid rozszerza się i kurczy w ciągu dnia.
„Rolą inżynierii wymiarowej jest kontrolowanie ustawień i określanie kątów i głębokości frezów, aby Extreme Fab mogła zapewnić precyzję wymaganą przez GE” — mówi Bonner.
Jeśli skid otrzymany przez GE nie będzie spełniał wymaganych specyfikacji, to może to mieć tragiczne skutki. „Samo wysłanie skida w jedną stronę kosztuje tysiące dolarów, więc jeśli musi on wrócić do Extreme Fab w celu wprowadzenia poprawek, to same dodatkowe koszty transportu mogą wynieść dziesiątki tysięcy dolarów” — wyjaśnia Bonner. Jeśli przeróbka wpływa na harmonogramy produkcji, może to również oznaczać znaczne kary finansowe.
Rozwiązanie
Przy każdym ruchu maszyny, przed każdym cięciem i po każdym działaniu, Dimensional Engineering dostarcza Extreme Fab precyzyjne pomiary w celu ustawienia frezarki, pozycji frezów i pozycji obrabianego przedmiotu w stosunku do statycznego, odprężonego stanu skida. Bez kontroli pomiarów spełnienie specyfikacji GE byłoby trudne, a nawet niemożliwe.
Bonner mówi, że korzysta z trackerów laserowych FARO oraz oprogramowania PolyWorks|Inspector™ firmy InnovMetric. „Używamy trackerów laserowych do wykonywania precyzyjnych pomiarów i PolyWorks do analizowania i przetwarzania zebranych danych, by nadzorować ciągle zmieniający się projekt” — mówi Bonner.
Dwuosobowy zespół Bonnera zaczyna od podstawowego ustawienia skida w stanie odprężonym. Korzystając z 50 punktów referencyjnych przyspawanych do obrabianego przedmiotu, tracker laserowy mierzy cechy bazowe skida, a PolyWorks tworzy ogólny układ współrzędnych. PolyWorks służy następnie do ustanowienia wielu lokalnych układów współrzędnych, które pozwalają zespołowi wyizolować ruch na pojedynczej podkładce montażowej przy zachowaniu relacji z całym skidem.
„Gdybyśmy nie mogli kontrolować pomiarów, uwzględniając zmianę pozycji trackera, mielibyśmy duży problem”.
Po ustawieniu i wypoziomowaniu frezarki, zespół Bonnera mierzy skid i pozycję frezu, aby uzyskać dokładne lokalizacje, których operatorzy używają do zaprogramowania głębokości i kąta cięcia. Po zakończeniu działania, przed wykonaniem kolejnego przejścia, ponownie dokonuje się pomiarów w celu sprawdzenia cięcia.
Ponieważ skid zmienia się wraz z temperaturą, zespół inżynierii wymiarowej przetwarza wszystkie dane pomiarowe przy użyciu dynamicznych funkcji kompensacji temperatury, które oferuje PolyWorks. Ta regulacja, w połączeniu z dokładną lokalizacją obrabianego elementu, pozwala operatorom zaprogramować ścieżki frezów względem skida w stabilnej temperaturze, a nie w aktualnej, dynamicznie zmieniającej się pozycji.
Ze względu na rozmiar skida i linię wzroku, trackery laserowe FARO pozycjonowano dziesiątki razy w ciągu 10 dni trwania projektu. Wprowadza to kolejną zmienną do precyzyjnej obróbki. Aby upewnić się, że wszystkie pomiary są precyzyjne względem wszystkich pozycji trackerów, zespół Bonnera wykorzystuje urządzenie do przesuwania PolyWorks oraz wiązanie w czasie rzeczywistym. Jak stwierdza Bonner: „gdybyśmy nie mogli kontrolować pomiarów, uwzględniając zmianę pozycji trackera, mielibyśmy duży problem”.
Aby zakończyć projekt, przeprowadzana jest kontrola końcowa, która potwierdza, że skid spełnia specyfikacje GE. „Zatwierdzamy i certyfikujemy każdy pomiar, zarówno podczas projektu, jak i przed wysyłką” — podsumowuje Bonner.
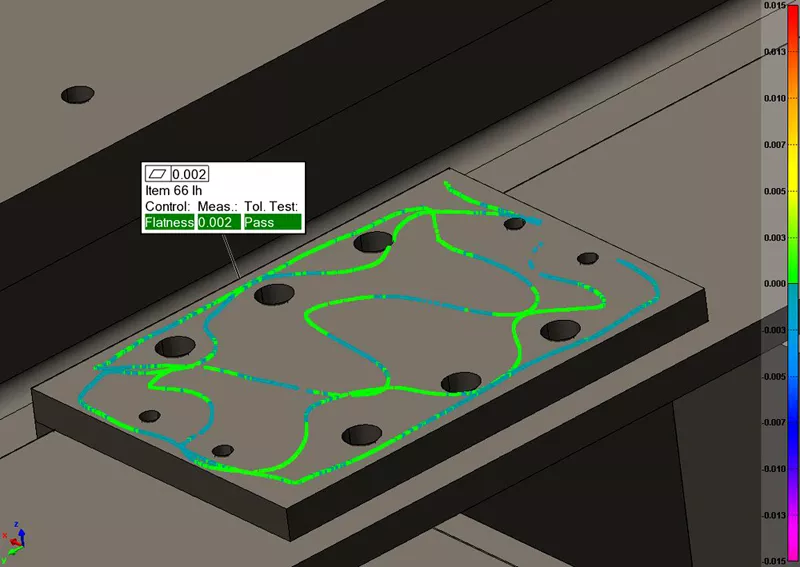
Wyniki kontroli końcowej potwierdzają płaskość powierzchni montażowej.
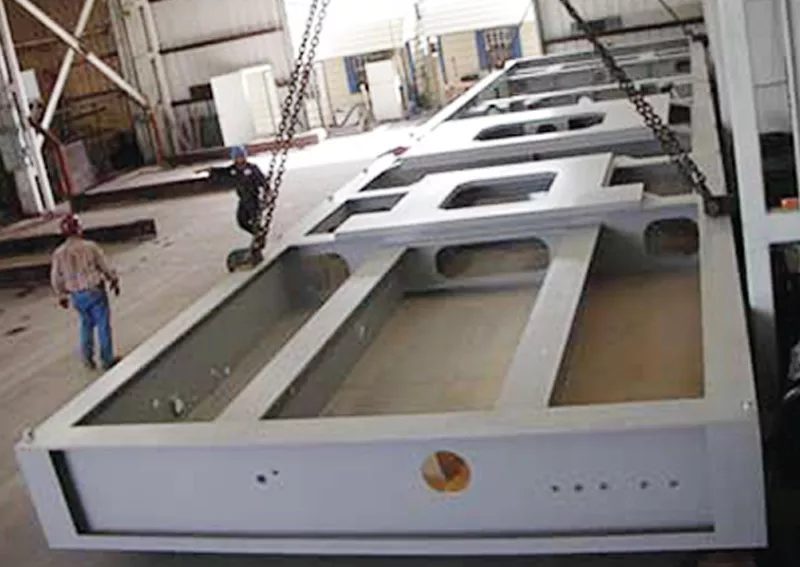
Wykończony skid gotowy do wysyłki do GE.
Korzyści
„Bez trackera laserowego i rozwiązania PolyWorks|Inspector nie moglibyśmy osiągnąć tego poziomu dokładności i precyzji, przynajmniej nie w wymierny sposób” — mówi Bonner. „Zajmujemy się tym od sześciu lat i pracowaliśmy na ponad 50 skidach. Żaden z nich nie musiał odbywać kosztownej podróży z powrotem w celu wprowadzenia poprawek”. W ciągu tych sześciu lat firma Dimensional Engineering otrzymała tylko dwa raporty o niezgodnościach (NCR): Jeden z nich dotyczył pojedynczego otworu niezgodnego ze specyfikacją, a drugi wynikał ze sprzecznych specyfikacji na rysunkach skida.
Inżynieria wymiarowa stosuje ten sam proces i narzędzia do innych dużych projektów, w tym do elementów pomocniczych dla pakietu LMS100, takich jak intercooler. „Techniki dotyczące skida wykorzystuje się do pozycjonowania dwóch 50-stopowych szyn montażowych chłodnicy podczas ich spawania, 120 otworów na kołnierzu montażowym chłodnicy oraz równoległości na kołnierzach wlotowych i wylotowych” — mówi Bonner. „Bez precyzyjnych pomiarów, które uzyskujemy z trackera laserowego FARO i PolyWorks, chłodnica nie pasowałaby do intercoolera, a intercooler nie byłby prawidłowo połączony z turbiną LMS100”.
Dzięki PolyWorks inżynieria wymiarowa może zapewnić, że ruchome cele są możliwe do opanowania, a obróbka na dużą skalę jest przewidywalna.