A Single Software Specialized in 3D Measurement and Analysis for all Measuring Devices
When Italian company Bruno Presezzi SpA, a specialist in mechanical machining, decided to add 3D scanning for dimensional control to other systems already being used, it chose PolyWorks® for the convenience of having a single software for all its measuring devices.
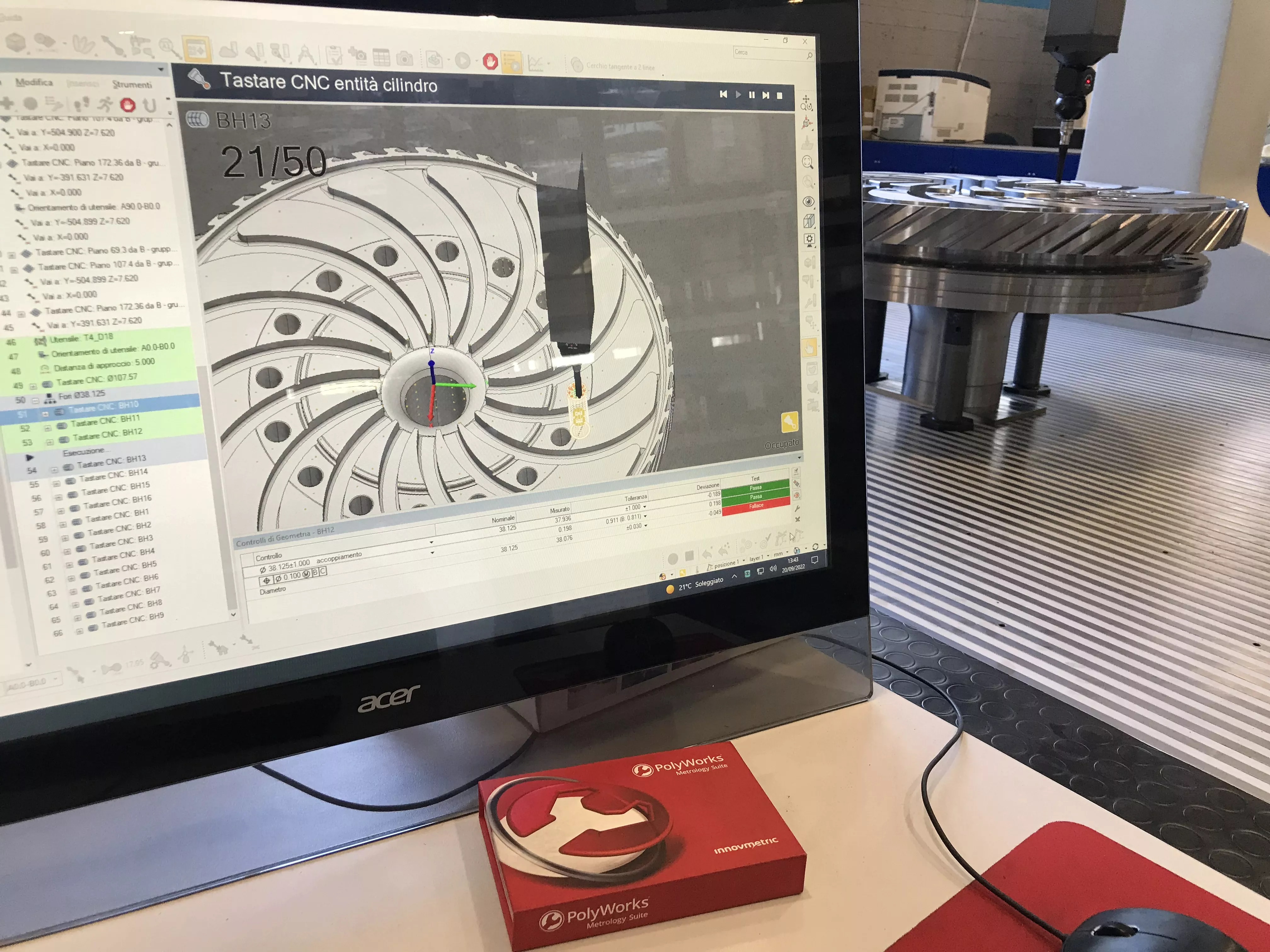
Final inspection of a compressor disc for a gas turbine by probing with a COORD3 Kronos CMM.
Bruno Presezzi is a flourishing company with 200 employees in Burago Molgora, located 20 km northeast of Milan, that operates in the metal engineering sector. One of its core businesses is the mechanical machining of large components, with very accurate tolerances, in addition to a carpentry division, again dedicated to large parts. Recently, they also became involved in the design and manufacture of systems for aluminum castings as well as compressor, steam, and hydroelectric turbines.
THE CHALLENGE
Bruno Presezzi represents an imposing and varied reality, with in-house operational structures that follow the design, assembly, mechanical machining, and carpentry activities, and everything that revolves around that. More specifically, it carries out dimensional quality controls on 100% of its production.
Quality requirements were growing, especially with regard to mechanical machining—clients were increasingly looking for detail and precision, particularly in terms of geometric, linear, and assembly tolerances.
So, their Quality Control department decided to purchase a MetraSCAN Black™|Elite optical CMM scanner from Creaform, a product on the frontier of technology with which they can acquire the complete form of the components they produce. The scanner takes millions of points and outputs a polygonal mesh accurately describing the measured surface.
The scanner, combined with a FARO laser tracker and a Kronos series CMM from COORD3, made for three measuring devices, each with its own native software. Over time, it became complicated for the operators to manage three different types of software, including even additional training. Bruno Presezzi went looking for a universal platform capable of managing all the measuring devices using a single software.
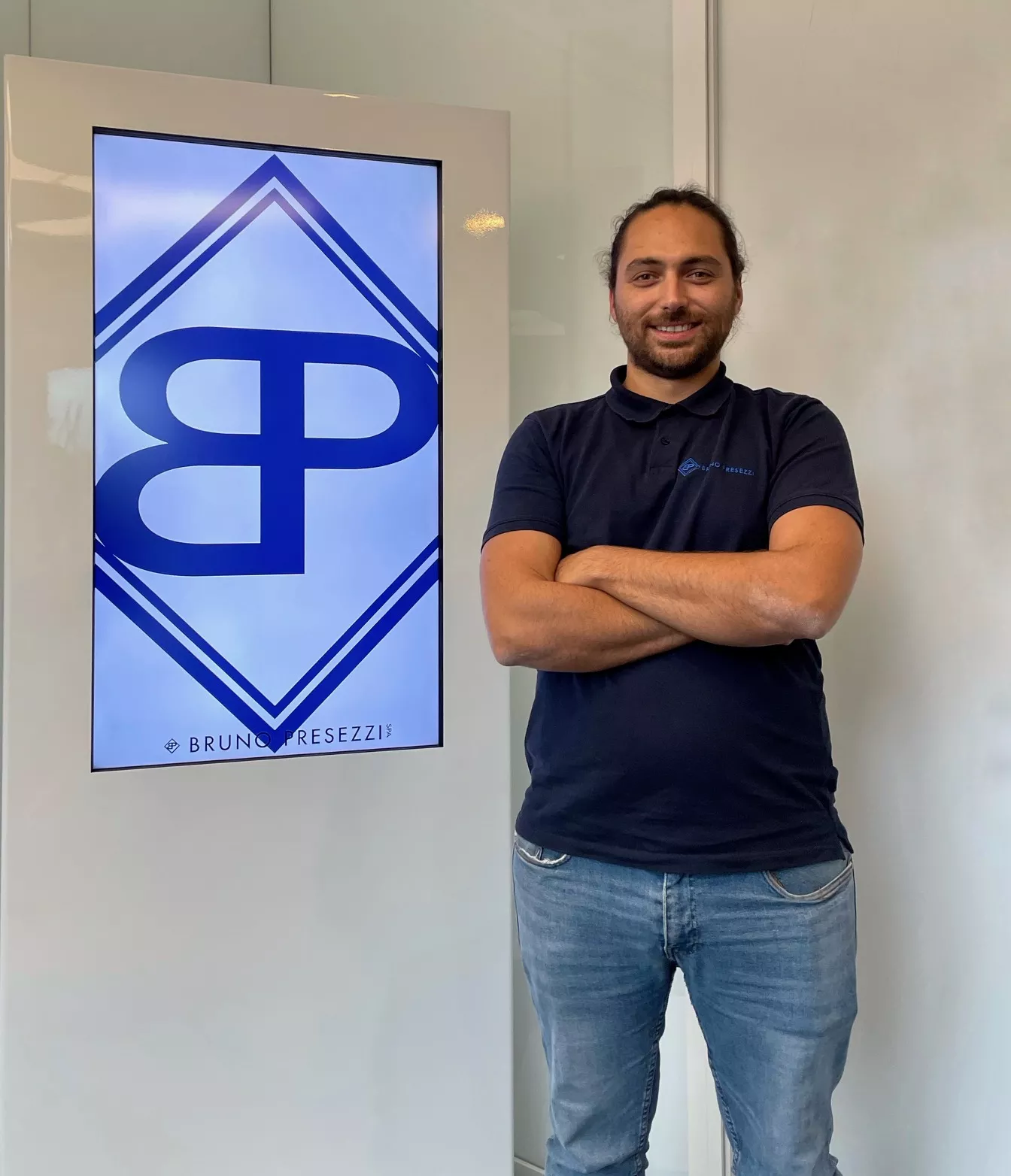
Sem Fantauzzi, Quality Control Manager at Bruno Presezzi.
THE SOLUTION
It was essential to be able to use the same software on all 3D measuring instruments. After extensive research, they decided to turn to PolyWorks® from InnovMetric, a Canadian company dedicated exclusively to intelligent 3D metrology software solutions, and to all satellite topics. And more specifically, PolyWorks|Inspector™, its module for dimensional analysis and quality control. And it is precisely in this context that a partnership was created with PolyWorks Europa Italia, a subsidiary of InnovMetric that sells PolyWorks and provides technical support to clients.
To use the software on three different devices Bruno Presezzi needed help, especially in the beginning, and PolyWorks Europa Italia came through for them by training every quality inspector who carries out dimensional checks. “Their support was essential for us,” comments Sem Fantauzzi, Quality Control Manager. “Indeed, it was, and still is. Their technical support is not just intended to maintain the software but also to find solutions. We appreciate this ongoing partnership with an expert in an accompanying journey to maximize the possibilities of PolyWorks for our processes.”
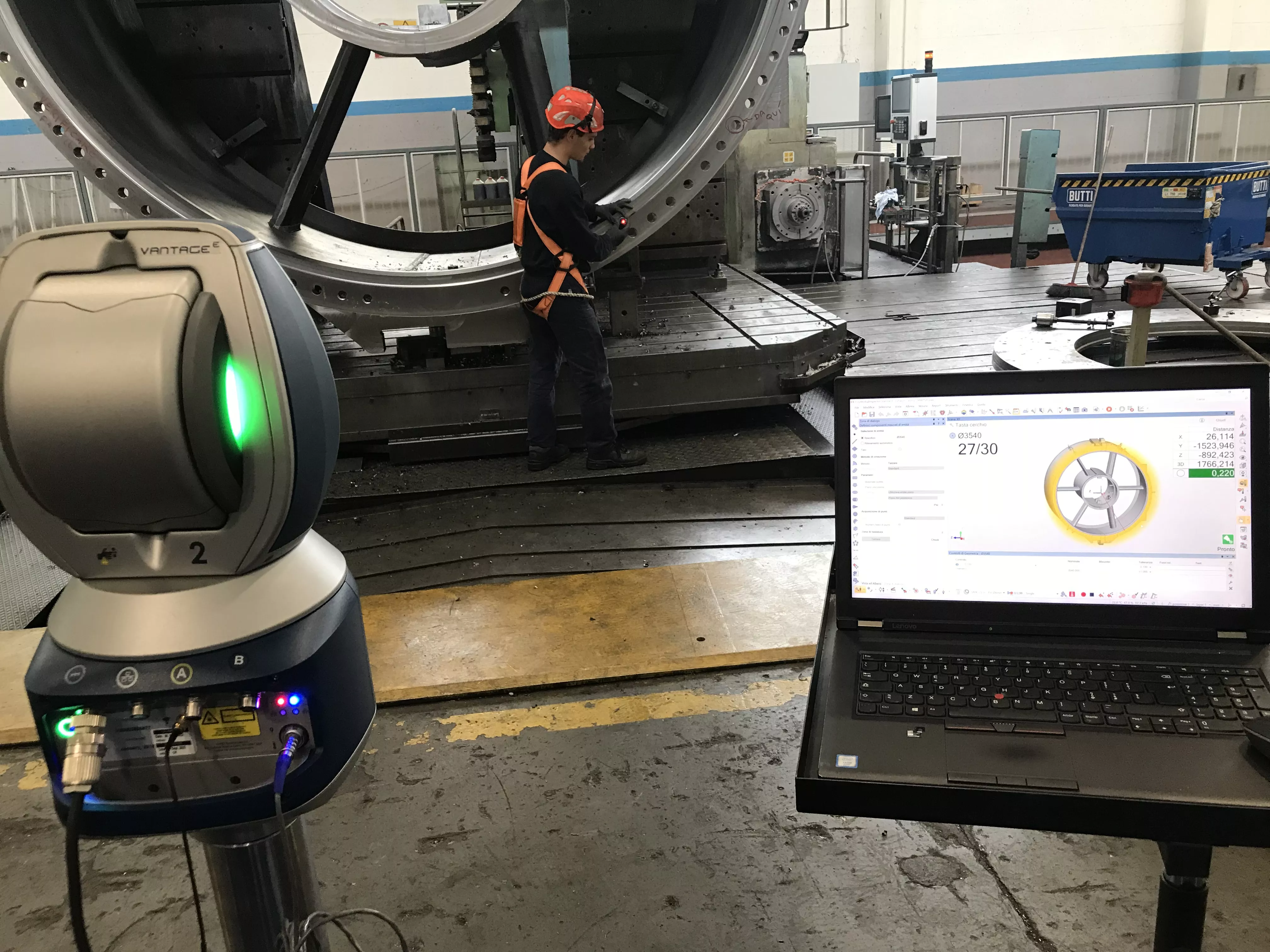
Final inspection with FARO laser tracker of a gas turbine exhaust case.
Fantauzzi explains, “For the past year, PolyWorks has been 100 percent operational in all our dimensional controls using our three measuring devices. And when we hire new employees, we provide an initial course to give them a basic knowledge of the software right away.”
Now, in addition to probing, scanning is a big part of their inspection processes. Fantauzzi points out, “We use it mainly for carpentry and raw components. The main advantage is that we no longer have to probe on the machine: we scan the blank, and if it doesn’t turn out to be suitable for the finished part, we move on to the next part without wasting time and money. Furthermore, unlike probing, which is always carried out on a limited number of points, with a 3D scan we capture millions of points, highlighting defects or anomalies previously impossible to analyze. PolyWorks interfaces perfectly with our scanner and handles those large scans very efficiently.”
THE BENEFITS
Says Fantauzzi, “The first benefit is using a single software to interface with our 3D measuring devices, which saves on training and brings a culture of shared knowledge within the quality control team. But there is even more. In addition to the practicality which we can enjoy every day using a single software, PolyWorks has opened the door to analyses and checks which we were not able to carry out before.”
He continues, “Another advantage is being able to use several measuring devices in the same inspection project. For instance, when a component has dimensions and features which can be checked with a scan, but a laser tracker is needed for a more accurate check on the inside, we can combine the measurements in the same project. The software actually works with all the measuring devices, and all the devices work in the same project, thanks to a series of customized measurements which can be added.”
Fantauzzi’s team has also benefited from PolyWorks’ multipiece inspection capabilities. “We always talk about the combination of data acquisition and data analysis, how one could not exist without the other. While we usually produce individual parts, one project involved the construction of 48 guide vanes for the Isola Serafini hydroelectric power station on the Po River. With the support of PolyWorks, we adapted the program to control the first piece, so that we could use it with all subsequent pieces. We thus avoided having to recreate a new program for each new piece, which greatly accelerated our processes.”
He also counts on PolyWorks’ powerful scripting capabilities to accelerate part inspection. “For a different client, we had to analyze geometric tolerances on turbine discs, which can have dozens and dozens of vane slots with particular shapes. With PolyWorks, we created macros: once the first slot was checked correctly, that could be repeated automatically for all the other slots. The possibility of creating macros is actually always envisaged, even in the basic versions of the software. They can be created either together with technical support, or independently if you have the necessary skills. A broad selection of helpful macros is available for download on the InnovMetric website according to your application needs. A versatility we greatly appreciate.”
In conclusion, Fantauzzi reflects on his experience with PolyWorks and his partnership with PolyWorks Europa Italia. “The software is indeed complete in all the analyses and all the structures on which we act. It has therefore broadened our horizons on the type of control required and the needs of our customers.”